The overhead hoisting systems are precisely engineered machines that are used for in-house logistics and transport of heavy materials. These cranes and hoisting devices are available in different sizes and shapes, and they can be fixed or moved around to suit the specific requirements of a warehouse. The best known examples of overhead cranes are single girder suspension machines and wall mounted trolleys with bridge girders/beams.
What are the multiple utilities of overhead cranes? Where are they mostly used?
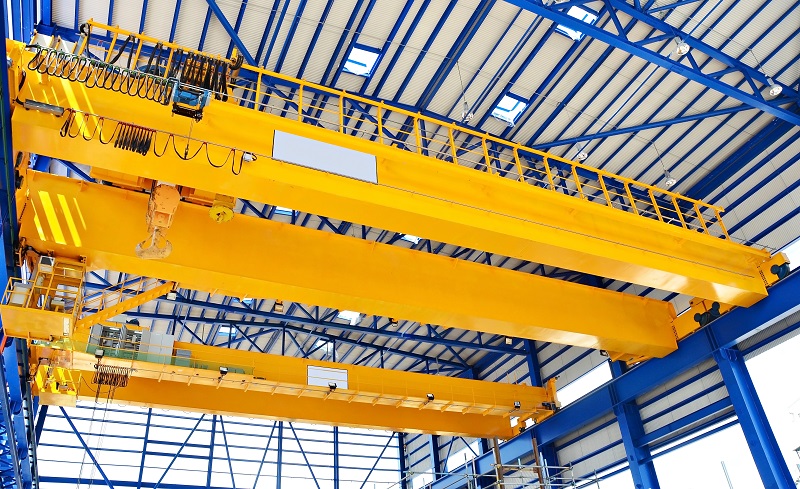
They are used extensively in large scale manufacturing units, mills, and production depots.
The popular and reliable overhead cranes have many important structures and components which can be designed, manufactured, configured and installed at indoor bays or outdoor locations like shipyards and power turbines. There are different types of overhead fixtures that have single or double beams, platforms, fixed and movable components, electrical system, and remote controls to achieve mobility and precision in loading.
Important and Sensitive Parts of a crane system must be checked before you hire a crane for commercial purpose:
The primary components and structural elements of the overhead cranes are listed below-
- The beams are directly wall mounted or they are installed on platform or runways.
- The indoor runways usually run from one end of the warehouse’s wall to another.
- One, two, or multiple beams, known as bridge girders, are mounted on to the runways or fixed to the walls.
- The girder’s movement is facilitated by components known as end truck, bumper, bridge drive, idler and drive wheels.
- This is the main structure that is found in the outdoor or in-house production units.
The loading, lifting, and unloading operations are carried out by trained workers through the following components that are fixed and configured on to the overhead cranes:
- One or more trolley frames that run the span of the bridge girders from wall to wall.
- Single or multiple hoists that are mounted on to the trolleys for lifting and moving the heavy materials using a remote-controlled device.
- Wire rope or chain hoist, hook block, pendant and cable complete the arrangement.
Installation Procedure
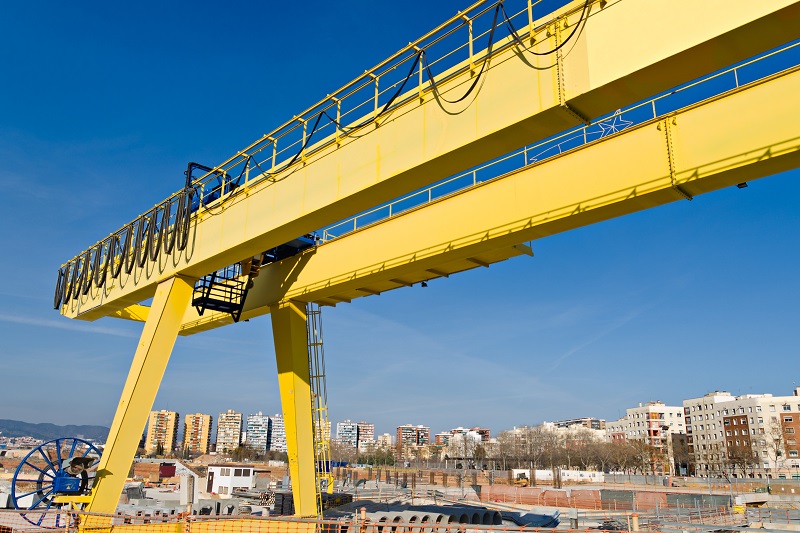
Modern overhead cranes have sophisticated and smart features that speed up the production process in assembly line and manufacturing units or warehouses. These heavy load lifting machines are safely fitted and tested by experienced installers who are completely well versed in the mechanical and technical aspects. The experts take 2 to 10 days for supplying all the components to the indoor site and finish the fixture to make it ready for production operations.
The safe and reliable installation of overhead cranes is a complex and time-consuming activity due to logistical demands, and the following sequence of actions are performed by distributors, mechanics, riggers, assemblers, and electrical technicians –
- Customer approaches the crane manufacturer with all the required specifications.
- The installer supplies a quote and specifies a time window to make the decision.
- The purchase order is completed, and the equipment is manufactured or assembled.
- A schedule is drawn, and the crane experts arrive at the warehouse for safety analysis and primary inspection.
- The building layout, electrical hazards, plumbing, and runway detail is evaluated.
- The scope of work is determined, and the components are delivered to the site.
- The suppliers and workers use semi-trucks, trailers, flatbeds, mobile cranes, scissor lifts, generators, fall and personal protective equipment.
- The installation is completed on time and the locks, safety devices, and load tests are performed for customer satisfaction.
There are different suppliers of overhead cranes available in the market, and commercial and industrial segments compare the features, basic utilities and prices of the cranes before they take the cranes on rent.